When Should Rough-In Plumbing Inspections Occur?
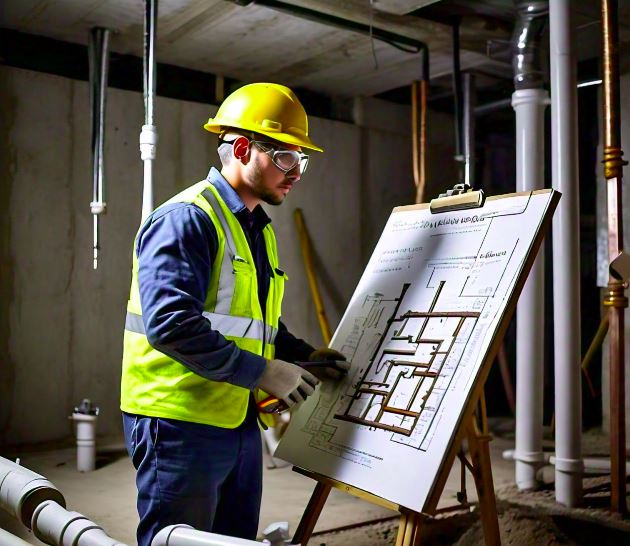
Rough-in plumbing inspections are a critical part of the construction process. They ensure that the plumbing system is correctly installed before it is covered by walls and floors. Proper timing and thorough inspections can prevent future issues, saving time and money. This guide will explain when rough-in plumbing inspections should occur and what they typically involve.
Key Stages for Rough-In Plumbing Inspections
1. After Framing is Complete
Rough-in plumbing inspections should occur after the building’s framing is complete. The framing provides the necessary structure for installing pipes and fixtures. Inspectors need to see the plumbing in relation to the building’s framework to ensure everything is correctly aligned and accessible.
2. Before Insulation and Drywall Installation
Inspections should be conducted before any insulation or drywall is installed. This stage allows inspectors to examine the entire plumbing system without obstructions. Once the walls and floors are covered, accessing and inspecting the plumbing becomes much more difficult and costly.
Specific Inspection Requirements
Drain, Waste, and Vent (DWV) System
For the DWV system, the rough-in inspection should include:
- Installation of Drain Lines: Ensuring that drain lines have the correct slope for proper drainage.
- Vent Pipes: Verifying that vent pipes are properly installed to prevent sewer gases from entering the building and to maintain pressure in the drainage system.
- Traps and Cleanouts: Checking that all traps and cleanouts are correctly placed for maintenance access.
Typically, the DWV system is pressure tested during this inspection. All openings except the highest point (usually on the roof) are sealed, and the system is filled with water or air to check for leaks.
Water Supply Lines
For water supply lines, the inspection should cover:
- Pipe Placement: Ensuring that pipes are correctly placed and securely fastened.
- Connections and Valves: Checking that all connections and shut-off valves are properly installed.
- Pressure Testing: Testing the water supply system to ensure there are no leaks. This involves pressurizing the system with air or water and monitoring for any pressure drops.
Common Issues Addressed in Inspections
Misalignment of Pipes
Inspectors check for the correct alignment of pipes with the planned fixture locations. Misaligned pipes can lead to improper fixture placement and functional issues.
Incorrect Sloping
The correct slope of drain pipes is crucial for efficient drainage. Inspectors ensure that pipes have the proper gradient to prevent blockages and slow drainage.
Inadequate Venting
Proper venting is essential to maintain pressure in the drainage system and to prevent sewer gases from entering the building. Inspections ensure that vent pipes are correctly installed and unobstructed.
Preparing for the Inspection
Ensure Compliance with Local Codes
Before scheduling an inspection, ensure that the rough in plumbing complies with local building codes. These codes vary by location but generally cover pipe materials, installation methods, and required tests.
Conduct Preliminary Tests
Perform preliminary pressure tests on the water supply and DWV systems to identify and fix any leaks or issues before the official inspection. This proactive step can save time and prevent delays.
Have Plans and Permits Ready
Ensure that all necessary plans and permits are available for the inspector. These documents help the inspector understand the project scope and verify that the installation complies with approved plans.
During the Inspection
Inspectors will typically:
- Verify Pipe Placement and Support: Check that pipes are correctly placed according to the plans and are adequately supported.
- Examine Connections and Fittings: Ensure all connections and fittings are secure and leak-free.
- Conduct Pressure Tests: Perform or witness pressure tests to check for leaks in the water supply and DWV systems.
- Review Compliance with Codes: Ensure that the installation complies with local building codes and regulations.
Post-Inspection Steps
Addressing Issues
If the inspector identifies any issues, they must be addressed before proceeding with construction. This may involve adjusting pipe placement, fixing leaks, or adding supports.
Scheduling Follow-Up Inspections
In some cases, follow-up inspections may be required to verify that issues have been resolved. Ensure that any necessary corrections are made promptly to avoid delays in the construction schedule.
Conclusion
Rough-in plumbing inspections are essential for ensuring the integrity and functionality of a building’s plumbing system. By conducting these inspections after framing and before installing insulation and drywall, potential issues can be identified and resolved early, preventing costly repairs later. Proper preparation and understanding of what the inspection entails can help ensure a smooth and successful inspection process.